Medical package testing: Stability testing
Life Science Outsourcing provides stability testing including real-time aging and accelerated aging and provides a free accelerated aging calculator.
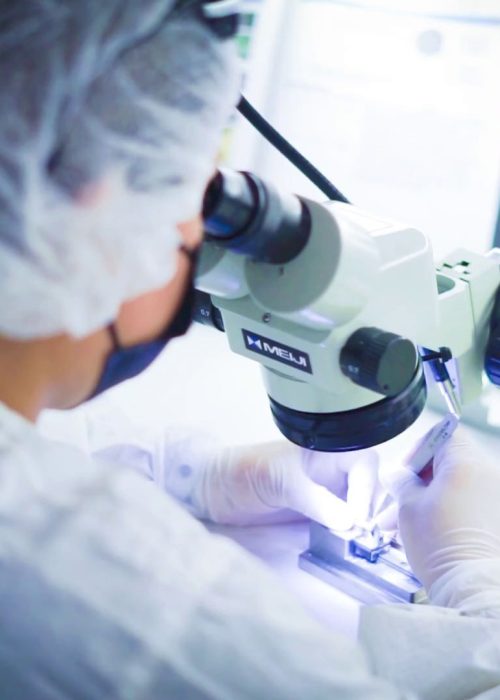
What is stability testing?
Medical device package stability testing is an important process that verifies safety and effectiveness of sterilized medical devices. It evaluates how well medical device packaging will maintain its integrity and performance over time under specified conditions. The main goal is to simulate real-world conditions that the package and device will encounter during storage and transportation.
Real-time aging and accelerating aging tests are often performed together to determine the shelf life and effects of aging on materials. Accelerated aging data is recognized by regulatory bodies as an acceptable means to generate data quickly, but this data is only accepted until those tests can be repeated on real-time product/package samples.
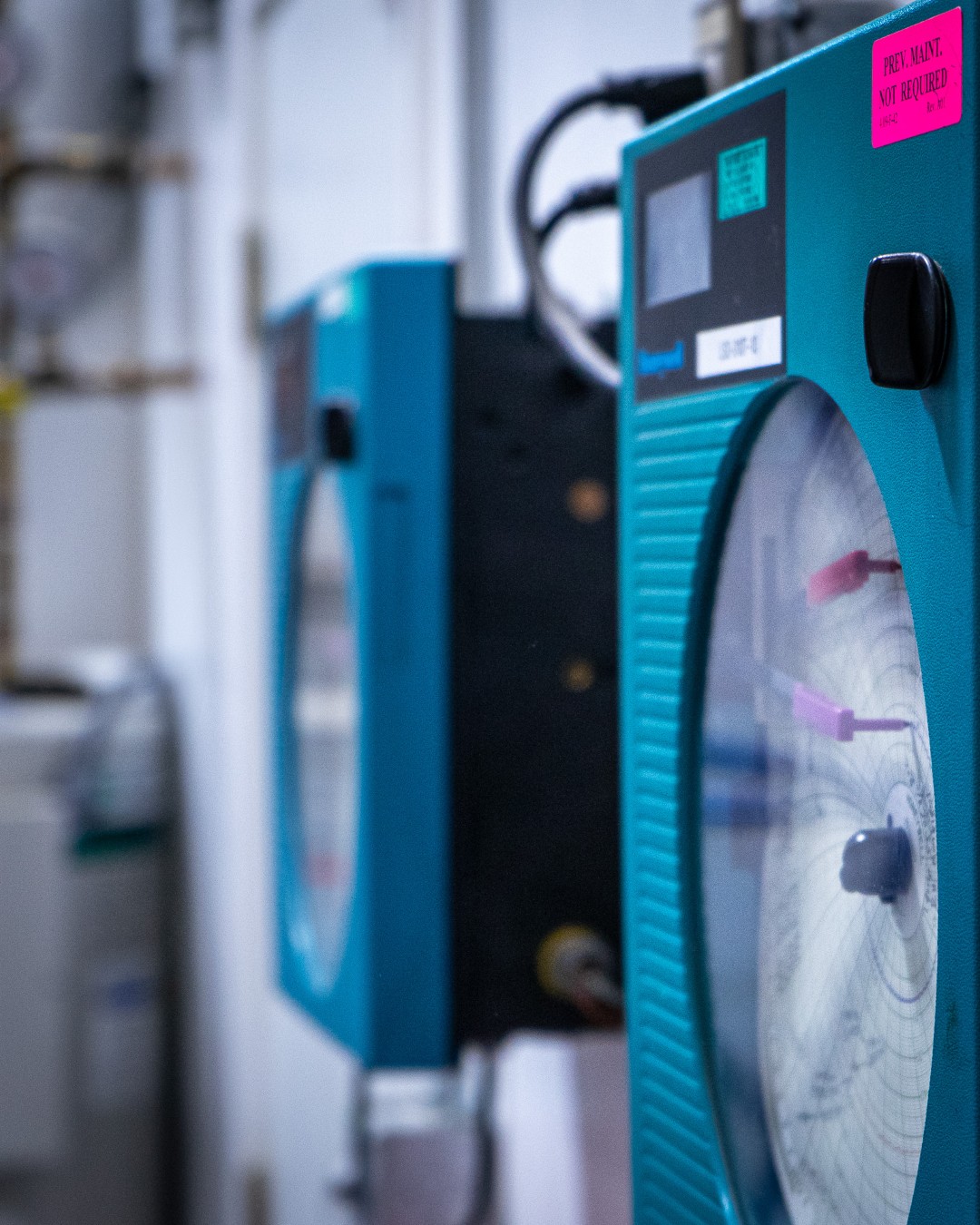
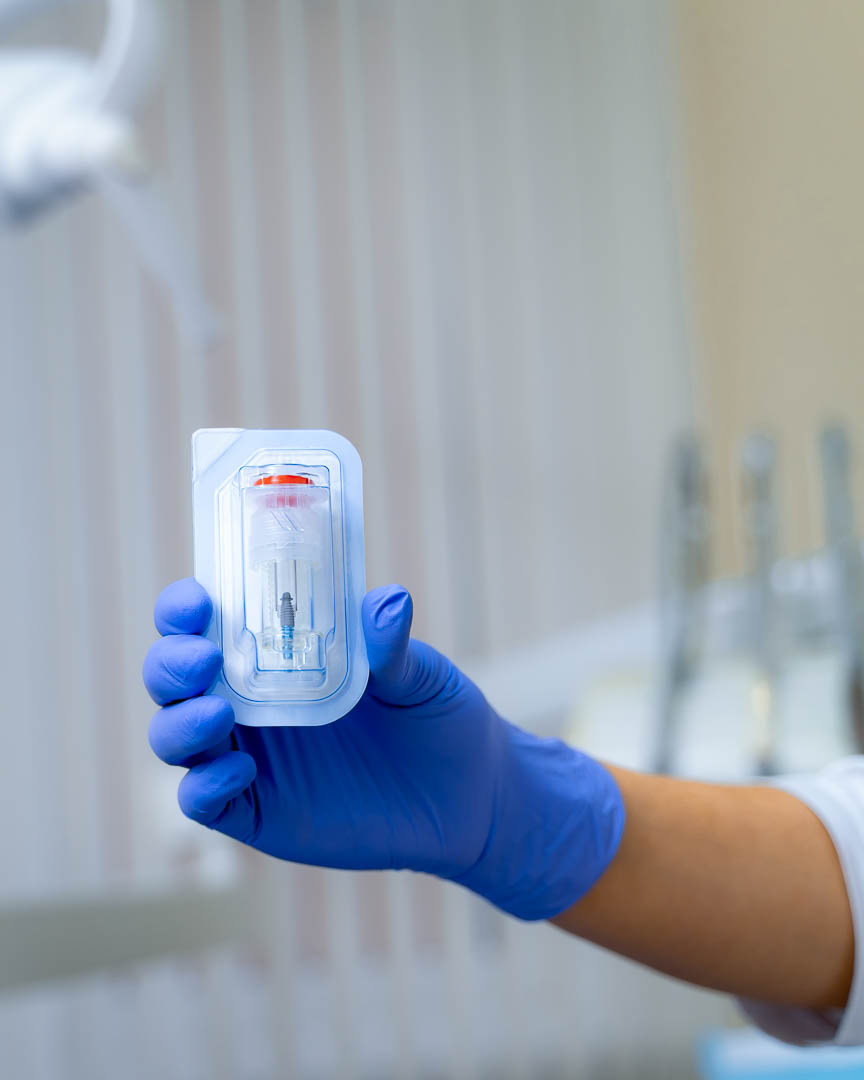
Who needs stability testing?
Any company that produces sterilized medical devices must conduct package stability testing. This includes manufacturers of surgical instruments, implants, diagnostic devices, and other medical products.
How does stability testing work?
Stability testing comprises real-time aging and accelerated aging methods.
Accelerated aging
Accelerated Aging is conducted by simulating the period claimed for product expiration. Simulation is achieved by varying temperature and humidity levels and thus exposing the packaged device to conditions it is expected to experience during its shelf life. The identified expiration date through accelerated aging is tentative until the results of real-time aging are obtained.
Calculation
Accelerated aging calculation is based on Arrhenius’ equation, which simply states that a 10°C increase in temperature doubles the rate of chemical reaction. Four variables are used in calculating the accelerated aging test duration. A calculator is provided below to easily explore different test scenarios.
- Test temperature (°C)
- Ambient temperature (°C)
- Q10 (reaction rate factor)
- Real-time equivalent (days)
Considerations
- Test temperature is typically between 50° to 60°C, most commonly 55°C.
- Ambient storage temperature is typically between 22°C to 25°C. 22°C results in the shortest test duration.
- Conservative / common Q10 is 2 for medical devices.
- Relative humidity (RH) is not a factor in the Arrhenius equation. However, RH should be kept under 20% so material is not damaged.
- The expiry date of a medical product is commonly based on its manufacture date. Therefore, some add an extra month to the aging study to allow for sterilization, etc. For example, a 12-month shelf life is simulated based on 13 months.
Real-time aging
Real-time aging tests are conducted by placing the test item on a shelf and allowing it to be exposed to typical storage conditions. Doing this will establish the item’s accurate expiration date and provide the best data to determine shelf life and the effects of aging on materials.
However, this test is not feasible in today’s market conditions in which products often become obsolete in a short time, and there is a need to shorten the product turnaround time. Time spent sitting on the shelf could prevent lifesaving devices from helping patients in need or could render the device obsolete before it reaches the market.
To work around this, real-time aging is performed in conjunction with accelerated aging tests. Accelerated aging is a testing method used to estimate the useful lifespan of a product when actual lifespan data is unavailable. This occurs with products that are relatively new and haven’t yet gone through their useful lifespan. A product can be released to market based upon results of successful accelerated aging of the product/package.
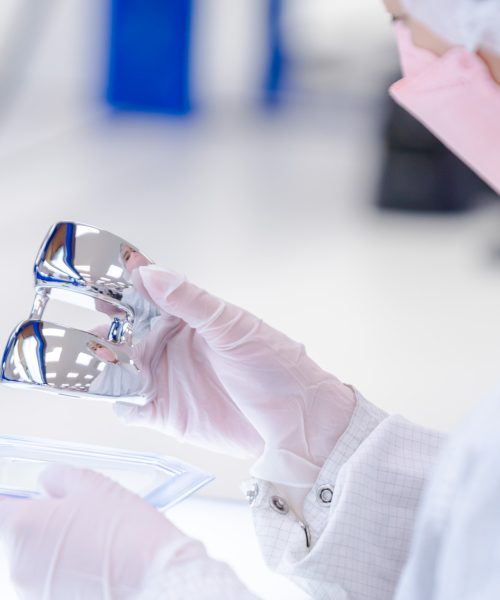
What standards apply?
The primary accelerated aging standards pertaining to sterile barrier systems for medical devices are:
- ANSI/AAMI/ISO 11607-1:2019
- ASTM F1980-16 (2016)
Why LSO?
As an FDA-registered and ISO 13485-certified contract manufacturing organization, Life Science Outsourcing (LSO) offers assembly, packaging, sterilization, and specialized capabilities in diagnostics packaging and design. Our unique business model combines comprehensive in-house services and extensive regulatory expertise, allowing us to provide the agility and flexibility needed to expedite market launches while standardizing the supply chain and minimizing risks.