Product sterility testing for medical devices
Product sterility testing is part of the sterilization validation process to show that devices would be free of viable microorganisms after the sterilization process is complete. Unlike biological indicator sterility testing, product sterility testing is performed on the device itself.
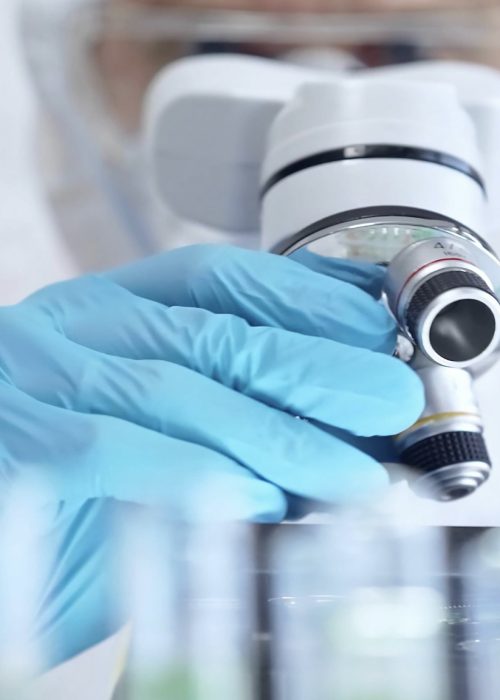
What is product sterility testing?
Sterility testing is used during validation to detect the presence of viable microorganisms that may remain in or on a medical device after undergoing a sublethal sterilization process. This type of testing is necessary to determine if the fully sterilized device will be sterile and safe for use.
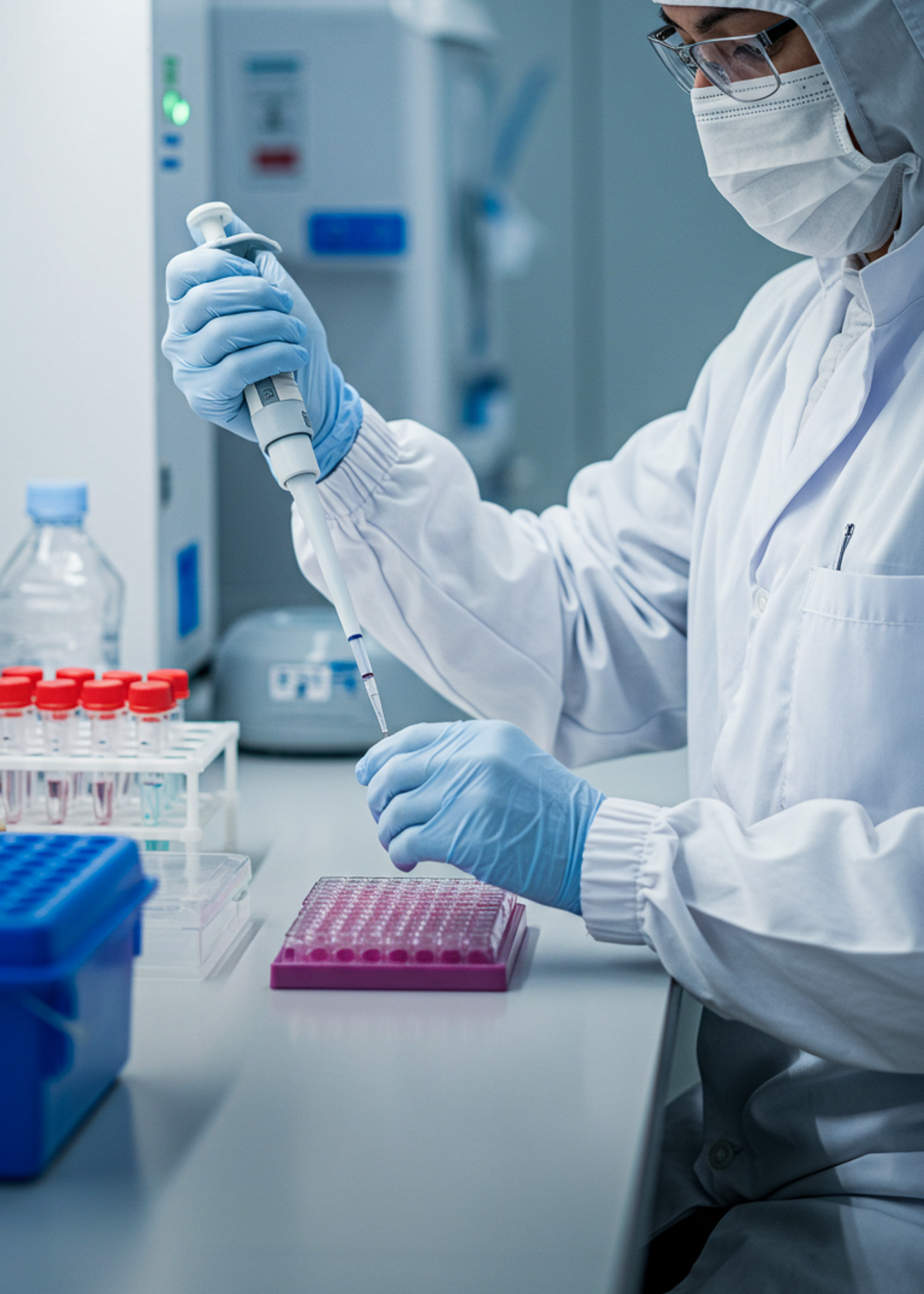
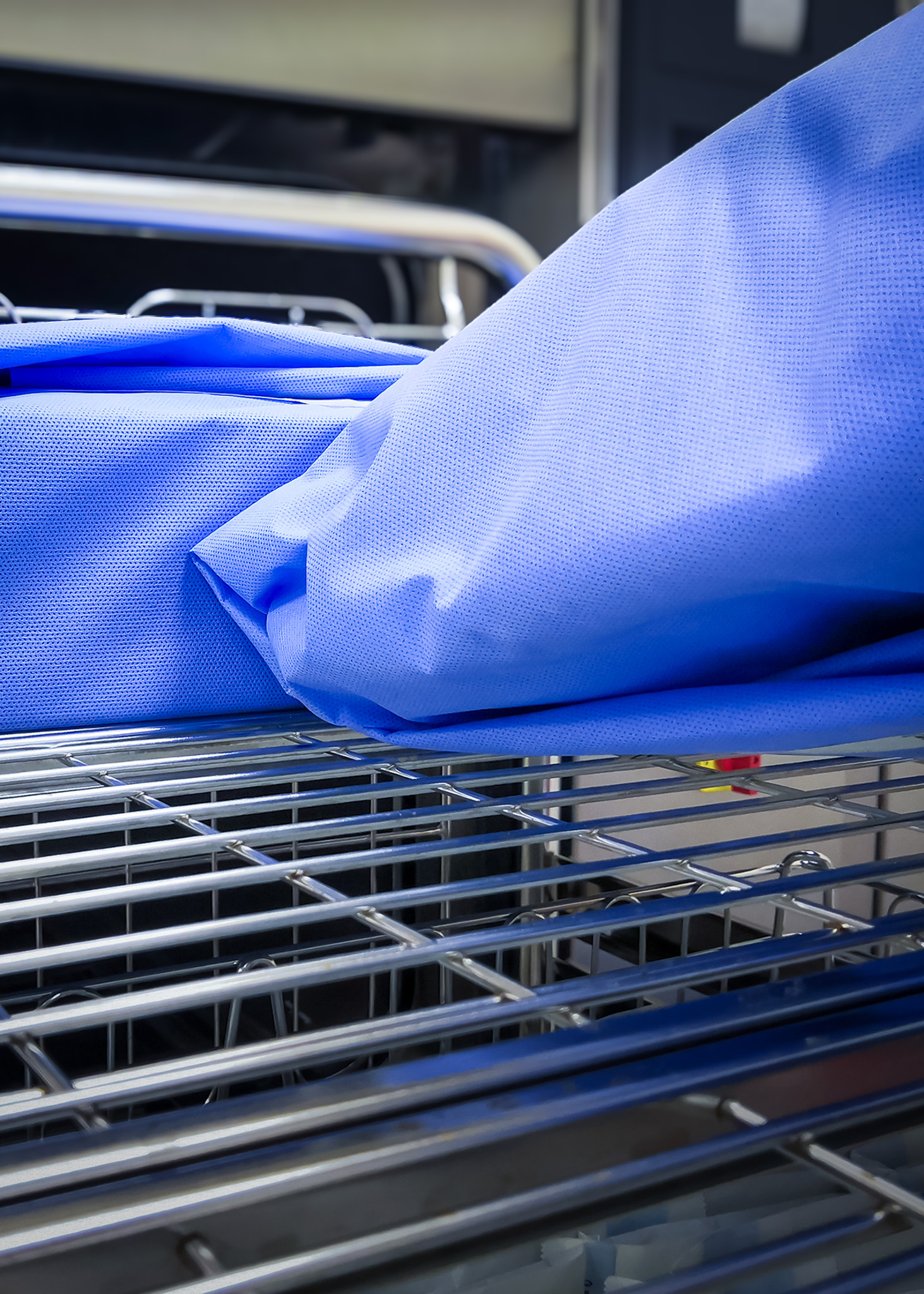
Who needs product sterility testing?
Medical device manufacturers use sterility testing to validate their sterilization process parameters.
How does sterility testing work?
Sterility testing requires controlled procedures to detect remaining viable organisms in or on a sterilized medical device:
Preparation
Representative samples are collected from each batch. Sample size is determined by batch size and regulatory requirements. Then testing is performed in a controlled environment like a cleanroom to prevent contamination.
Testing methods
The samples are then tested using one of two methods: Direct inoculation, or membrane filtration, each of which has several options.
Interpretation of results
The results are either negative (no growth) or positive (growth). If microbial growth is detected, an investigation may be triggered to determine any source of contamination and potential corrective actions.
Documenting and reporting
This step involves record keeping of all observations, test conditions and results, and detailed reporting about the samples tested, methods used, incubation conditions, and results.
Regulatory compliance
The final step is validation and routine testing for regulatory requirements, and quality assurance to demonstrate quality standards compliance.
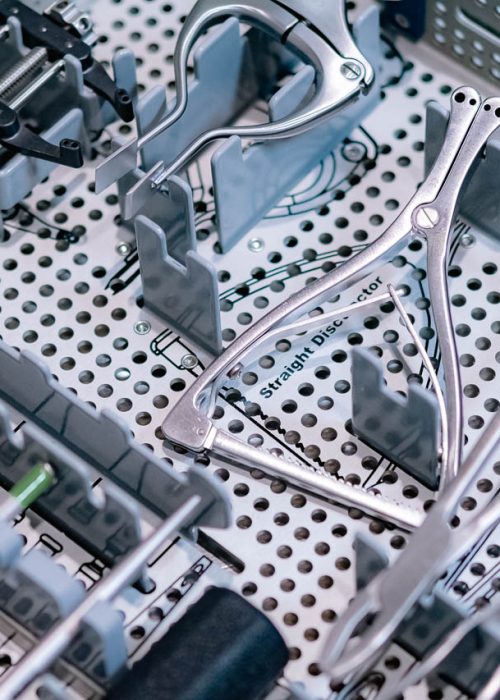
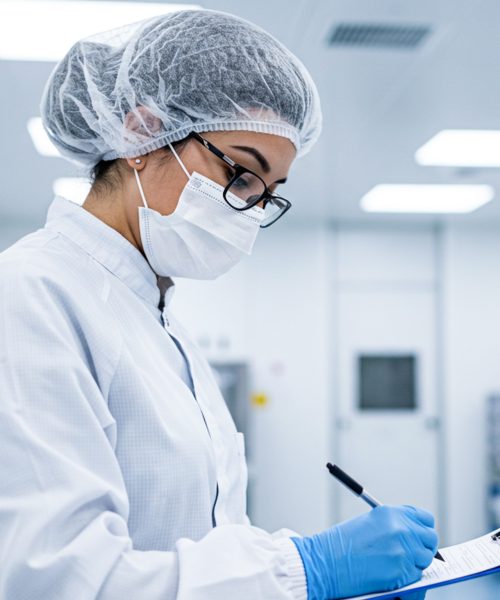
What standards apply?
ISO 11737-2 and USP <71> have guidelines on how to perform sterility tests.
Why LSO?
As an FDA-registered and ISO 13485-certified contract manufacturing organization, Life Science Outsourcing (LSO) offers assembly, packaging, sterilization, and specialized capabilities in diagnostics packaging and design. Our unique business model combines comprehensive in-house services and extensive regulatory expertise, allowing us to provide the agility and flexibility needed to expedite market launches while standardizing the supply chain and minimizing risks.