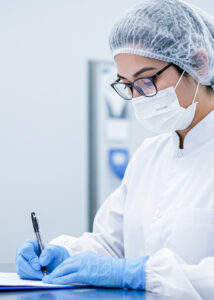
Your go-to resource for expert insights on design, manufacturing, assembly, packaging, sterilization, validation, and program management. Curated for medical device manufacturers, our Learning Center features the latest industry trends, best practices, and in-depth guidance from experienced professionals. Stay ahead with blogs, white papers, one-pagers, and company updates - all in one place.
A growing number of medical device innovations are introduced each year to equip medical professionals with solutions designed to enhance patient health. A critical aspect of these devices is sterilization, which ensures the eradication of pathogens to prevent healthcare-associated infections (HAIs). HAIs are prevalent in about 1 in 31 hospital patients in the United States.1 Annually, sepsis was indicated in approximately 1.7 million cases, or 6% of hospitalizations, culminating in 270,000 fatalities.2 Proactive measures, with sterilization at the forefront, are paramount for bolstering patient safety and minimizing the detrimental repercussions of HAIs.
Medical device packaging isn’t just about encasing a product – it’s an intricate balance of design, sterile barrier defense, and regulatory adherence. This white paper expands on the nuances of creating a robust medical device packaging strategy, emphasizing its purpose in safeguarding products and facilitating ease-of-use. Central to this is the critical role of the sterile barrier system, serving as the first line of defense against contaminants and pathogens.
Medical device package design can be a complex process that requires significant time and budget investments. Medical device manufacturers have increasingly turned to pre-validated packaging to mitigate such challenges. Pre-validated packaging has become a useful tool with considerable advantages over traditional custom-built packaging and can streamline the packaging process to prevent supply chain issues and deliver products to market faster, with reduced costs and fewer testing requirements.
As an FDA-registered and ISO 13485-certified contract manufacturing organization, Life Science Outsourcing (LSO) offers assembly, packaging, sterilization, and specialized capabilities in diagnostics packaging and design. Our unique business model combines comprehensive in-house services and extensive regulatory expertise, allowing us to provide the agility and flexibility needed to expedite market launches while standardizing the supply chain and minimizing risks.
Life Science Outsourcing is an FDA registered and ISO 13485 certified full service Medical Device Contract Manufacturer.
We improve our products and advertising by using Microsoft Clarity to see how you use our website. By using our site, you agree that we and Microsoft can collect and use this data. Our privacy notice has more details.
Receive the latest infographics, guides, and blog updates for medical device manufacturing, package testing, and sterilization.